If you are looking to build a workshop shed, you will likely need a concrete floor. If so, you may be wondering what thickness floor you need and how much it will cost. The answer is; it depends.
May 23rd, 2024
2 min read
By Brad Person
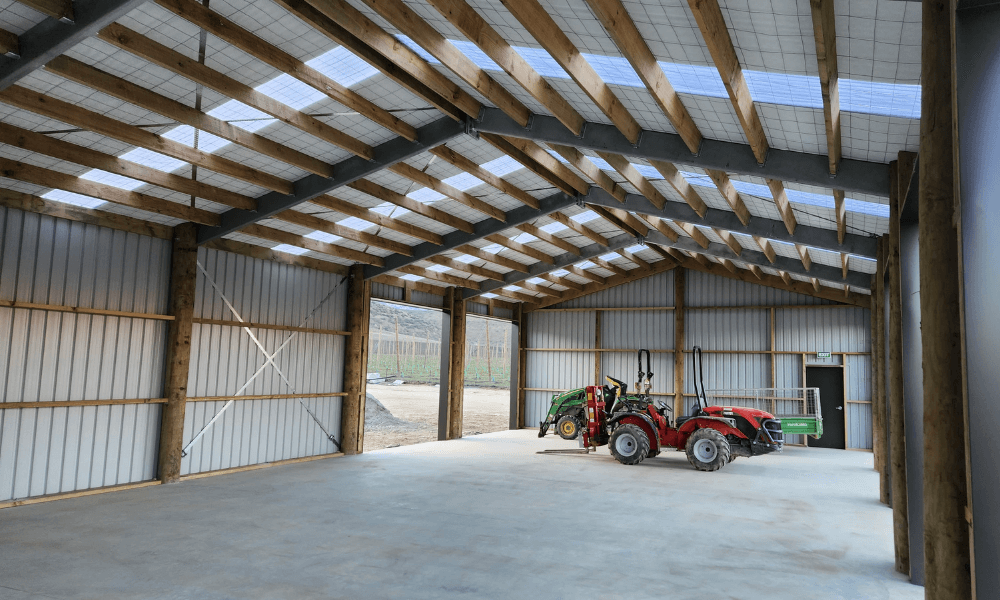