If you think back in time for a moment, there’s a high chance you can recall a story from a friend about a shed severely damaged in a big storm or strong wind. The doors blew in, part of the roof ...
February 7th, 2023
4 min read
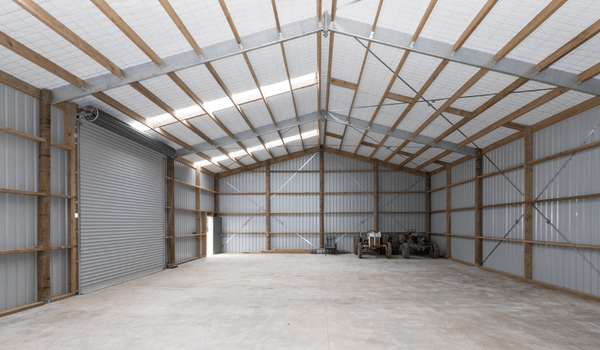